引言:
数字化转型中的隐形战场
在离散制造业的生产车间里,一台设备的停机可能造成每小时数十万元的损失,但比这更隐蔽的危机,是深藏在ERP、MES、PLM等系统中的数据断层。某汽车零部件企业曾因12家工厂使用5套不同的物料编码规则,导致跨部门协作效率下降40%;某飞机制造商因BOM清单与工艺参数不匹配,造成近亿元订单返工。这些真实案例揭示了一个残酷现实:数据孤岛正在蚕食制造企业的利润与竞争力。
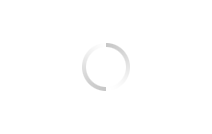
主数据管理:离散制造业打破数据孤岛的“黄金钥匙"" width="1191" height="823" title="
主数据管理:离散制造业打破数据孤岛的“黄金钥匙"" align="" />
一、离散制造业的数据治理困局
1.1 多系统并行引发的"数据巴别塔"
离散制造企业的数据孤岛往往源于多代系统的叠加:
物料编码混乱:同一型号螺栓在采购系统标注为"M10×50",生产系统显示为"螺栓-10-50"
BOM版本失控:某工程机械集团因设计端未及时同步变更数据,导致3个生产基地使用不同版本工艺参数
供应商信息失真:某装备制造企业因供应商银行账户信息未同步,错失6000万元订单
1.2 数据质量黑洞吞噬企业利润
行业调研显示,离散制造企业因数据问题导致的隐性成本高达营收的3%-5%,具体表现为:
采购成本虚高:某新能源企业通过主
数据清洗减少35%冗余SKU
生产效率折损:某军工企业因工艺参数传递错误,设备空转率长期高于12%
合规风险累积:某汽车厂商因供应商主数据缺失18%关键字段,面临供应链审计风险
二、主数据管理的战略价值重构
2.1 从成本中心到价值引擎的蜕变
主数据管理为离散制造企业创造三重核心价值:
降本增效:某航空企业统一物料编码后,采购成本降低17%,库存周转率提升25%
风险控制:某军工集团通过供应商主
数据标准化,质量追溯响应速度提升6倍
智能决策:某车企结合设备主数据与IoT传感器,实现92%的预测性维护准确率
2.2 技术革新:低代码平台重构治理范式
传统开发模式下需6个月完成的物料主数据模型,通过低代码平台可缩短至3天。行业领先的解决方案已实现四大突破:
敏捷建模:电池组件分类体系搭建周期从3个月压缩至2周
智能治理:自动识别90%重复供应商记录,BOM校验准确率超95%
生态集成:实现与SAP、金蝶等系统的分钟级数据同步
全生命周期管理:数据变更审批周期从7天缩短至4小时
三、破局路径:从顶层设计到落地实践
3.1 三步走实施方法论
诊断阶段(2-4周): 通过自动化工具扫描10万+存量数据,识别物料分类错误率23%等核心问题
体系构建(4-8周): 建立三级治理组织架构,制定包含32项标准的《主数据管理白皮书》
平台落地(8-12周): 完成15个系统对接,实施200+清洗规则,合并去重数据5万余条
3.2 分场景解决方案矩阵
针对不同细分领域提供定制化服务:
汽车制造:实现2000+供应商主数据统一管理,采购效率提升40%
航空航天:10万+零部件编码标准化,BOM变更传递时间缩短至30分钟
电子制造:构建覆盖5000+工业标准的语义网络,工艺纠错准确率提升80%
四、未来战场:AI驱动下的治理革命
4.1 技术演进三大趋势
认知智能:通过自然语言交互自动修复90%编码冲突
联邦学习:在保障隐私前提下优化库存预测准确率28%
数字孪生:3D建模还原生产流程,关键参数预测误差小于2小时
4.2 生态系统级协同创新
行业级解决方案已实现三大突破:
实时数据同步:5G技术实现设备数据毫秒级同步,OEE提升15%
区块链存证:建立不可篡改的数据变更存证链
知识图谱应用:覆盖389个数据节点的质量追溯体系
五、行业实践者的价值创造
深耕制造业数据治理领域的企业,通过"行业化+低代码"双引擎驱动,已帮助客户实现显著效益:
5.1 核心技术优势
预置行业模板:200+数据模型库缩短60%实施周期
BOM智能管理:10层复杂结构可视化编辑,冲突预警准确率95%
混合部署架构:满足军工等特殊行业的安全合规要求
5.2 实证客户价值
某汽车集团物料编码重复率从35%降至0.8%,年采购成本减少2.3亿元
某飞机制造商设计变更响应速度提升6倍,关键设备故障率下降35%
某白酒企业构建全链路追溯体系,包装材料浪费减少22%
结语:数据智能时代的生存法则
在工业4.0浪潮下,主数据管理已从"锦上添花"转变为"生存刚需"。选择具备行业积淀、技术生态开放、持续服务能力的解决方案,将成为制造企业数字化转型的分水岭。通过"低代码+AI"的创新组合,中国企业正跨越从数据治理到数据智能的鸿沟——让每一组编码、每一份BOM都成为驱动高质量发展的数字基因。
(部分内容来源网络,如有侵权请联系删除)